精益生产(lean production)是源自丰田生产方式的一种管理哲学。
丰田公司在探索新的生产模式过程中发现,小批量生产比大批量生产成本更低,原因有两个:
- 小批量生产不需要大量的库存、设备和人员
- 在装配前,只生产少量的零件,发现错误可以立即更正
根据这两个原因,丰田公司得出结论,应该将产品的库存时间控制在2个小时以内,即JIT(Just In Time,准时生产方式)和零库存的雏形,这就是精益理念的起源。
当下,国内生产企业的发展正在受到浪费问题的严重制约,资源投入与产出比例不相匹配,成本居高不下,且产品质量不能保证。
精益生产(lean production)就是解决浪费问题,提高企业生产效率,增强企业竞争力的一把钥匙。其核心思想就是最大限度地细化工作流程,消除浪费和一切非增值活动,以最小的投入获得最大的产出,向市场提供成本最低,质量最好的产品,以满足市场的需求。
如何做到精益生产
要有效落地精益生产管理,需要在两个层面作出努力。
第一层面在于企业内部。从管理者到一线员工都要明确精益生产的管理方式,各级管理者认可,精益化管理工作才能稳步推进,员工的参与程度直接决定精益生产能否取得实效,具体涉及六大关键因素:管理者认知、员工积极性、推行顺序、精准化切入点、树立标杆、营造氛围。
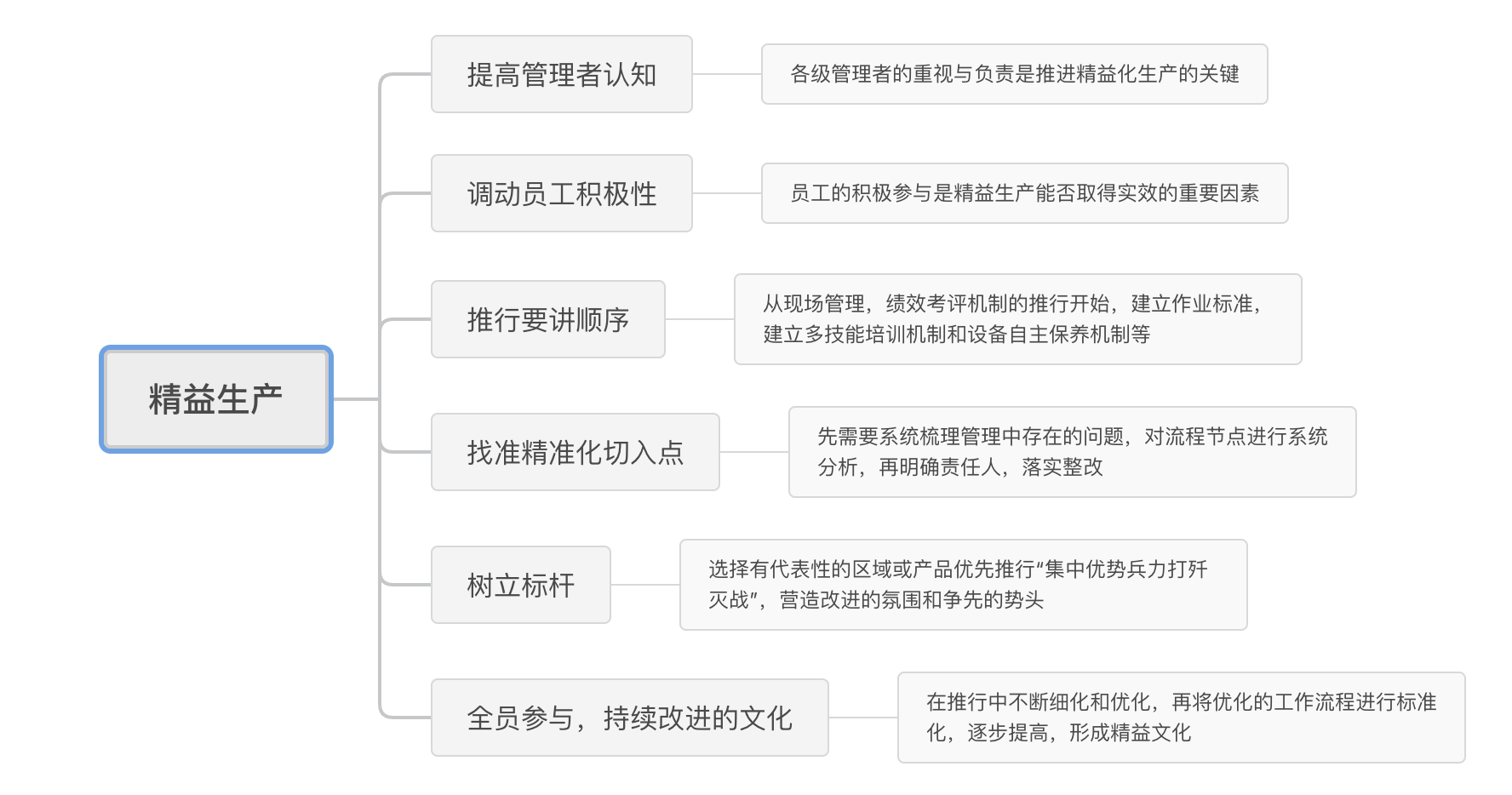
第二层面在于“工具”。欲善其事,必利其器。即使企业全体员工都明确精益生产的目标,若没有一个高效好用的工具仍会走弯路,难见实效。轻流根据精益生产的六大板块:生产现场管理、品质管理、设备管理、采购与仓储管理、生产安全管理、成本控制管理上线了相应的解决方案模版,帮助制造业企业能够顺利实施精益生产。

CI(合理化建议)
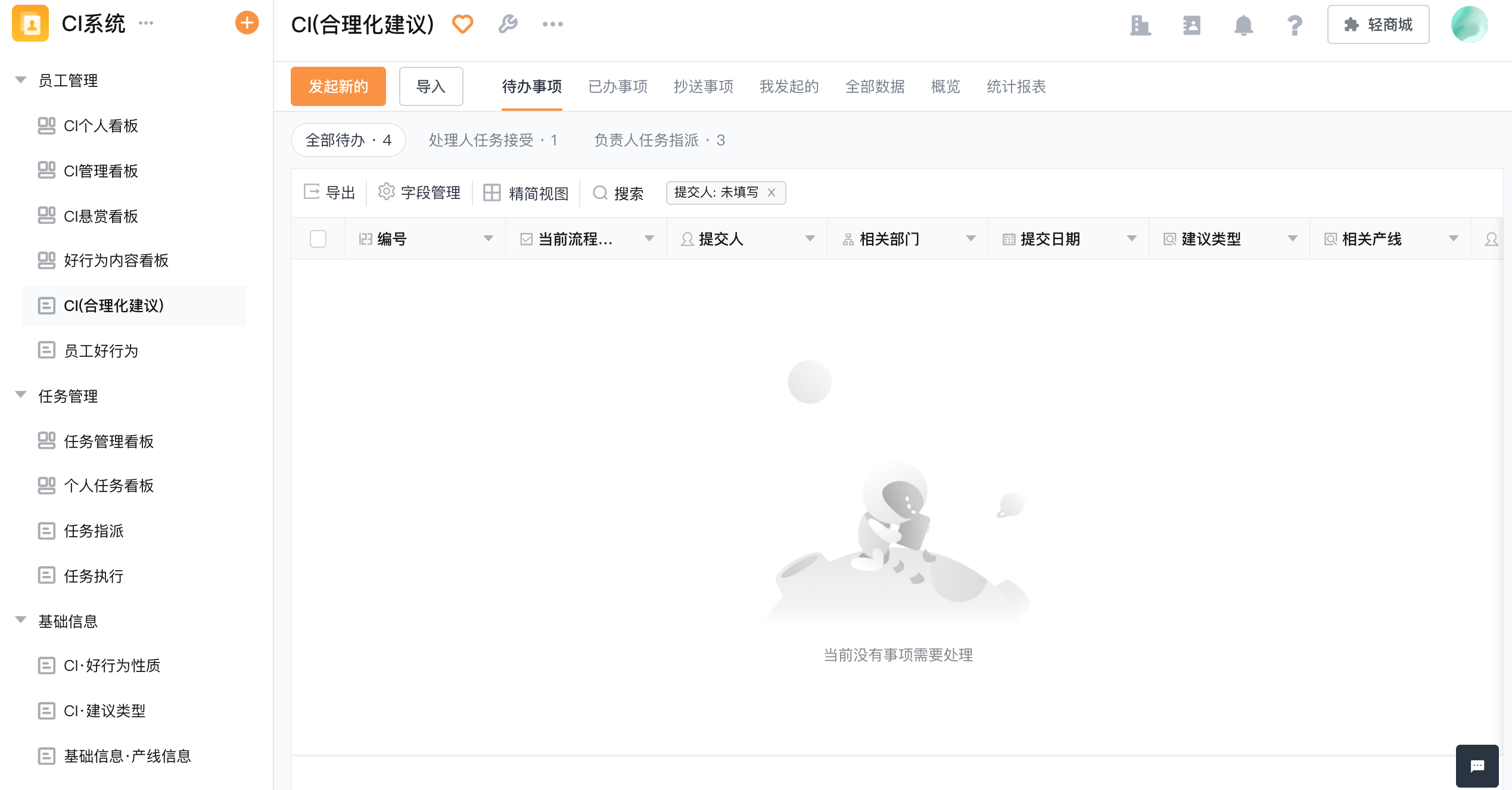
合理化建议的核心本质是持续改善。不管是生产设备现场、生产现场、现场管理,企业员工和管理层都能积极参与进去,通过【CI合理化建议】提建议,共同帮助企业提升效率。所提建议会自动同步到管理层的【员工管理】模块,企业可以采用积分制的方式,鼓励员工提建议。
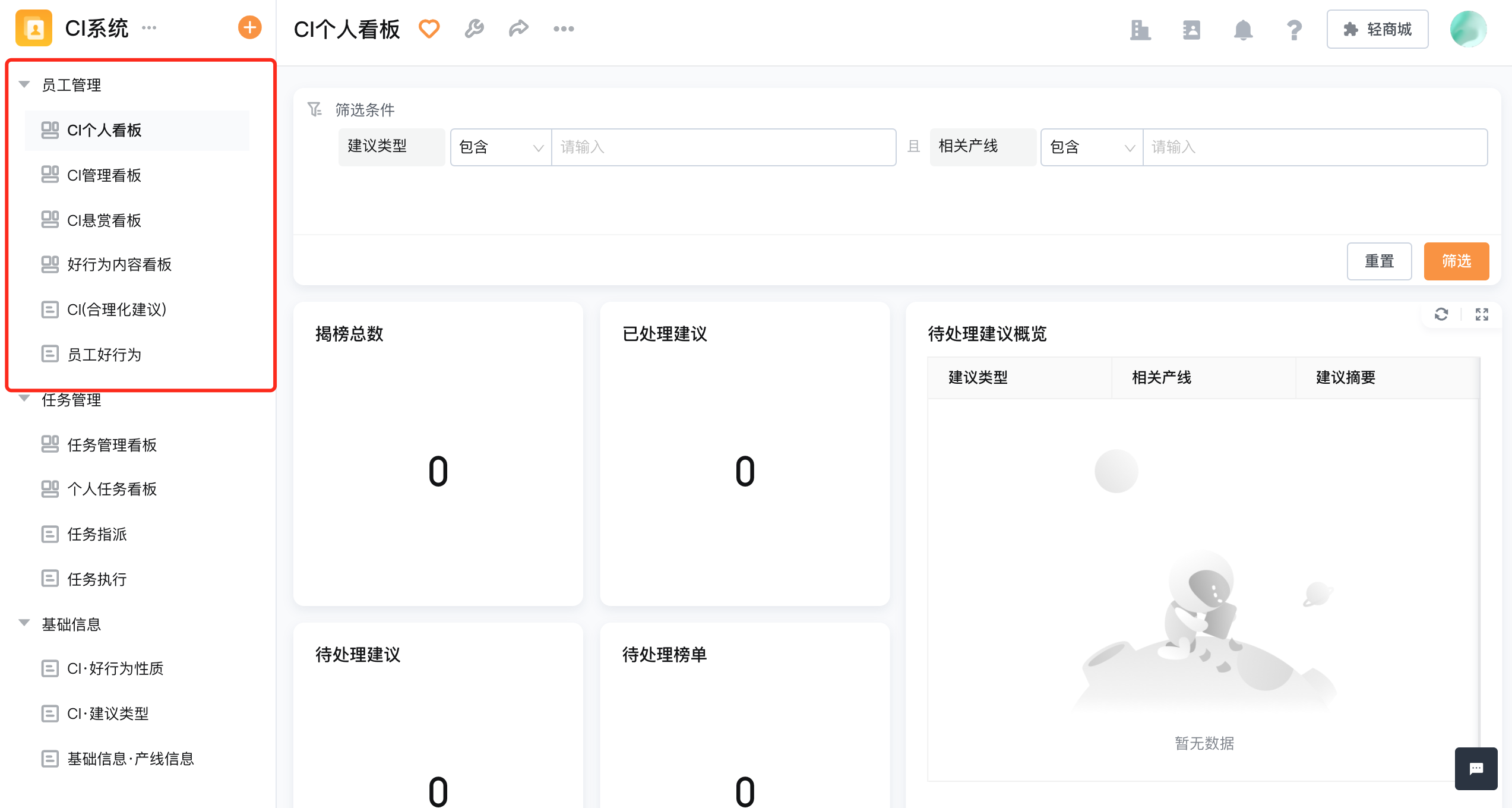
QMS质量管理系统
质量管理对于制造业企业来说相当重要,维护产品口碑,维护销量,是否能持续让产品在市场站稳脚跟都与质量管理直接相关。
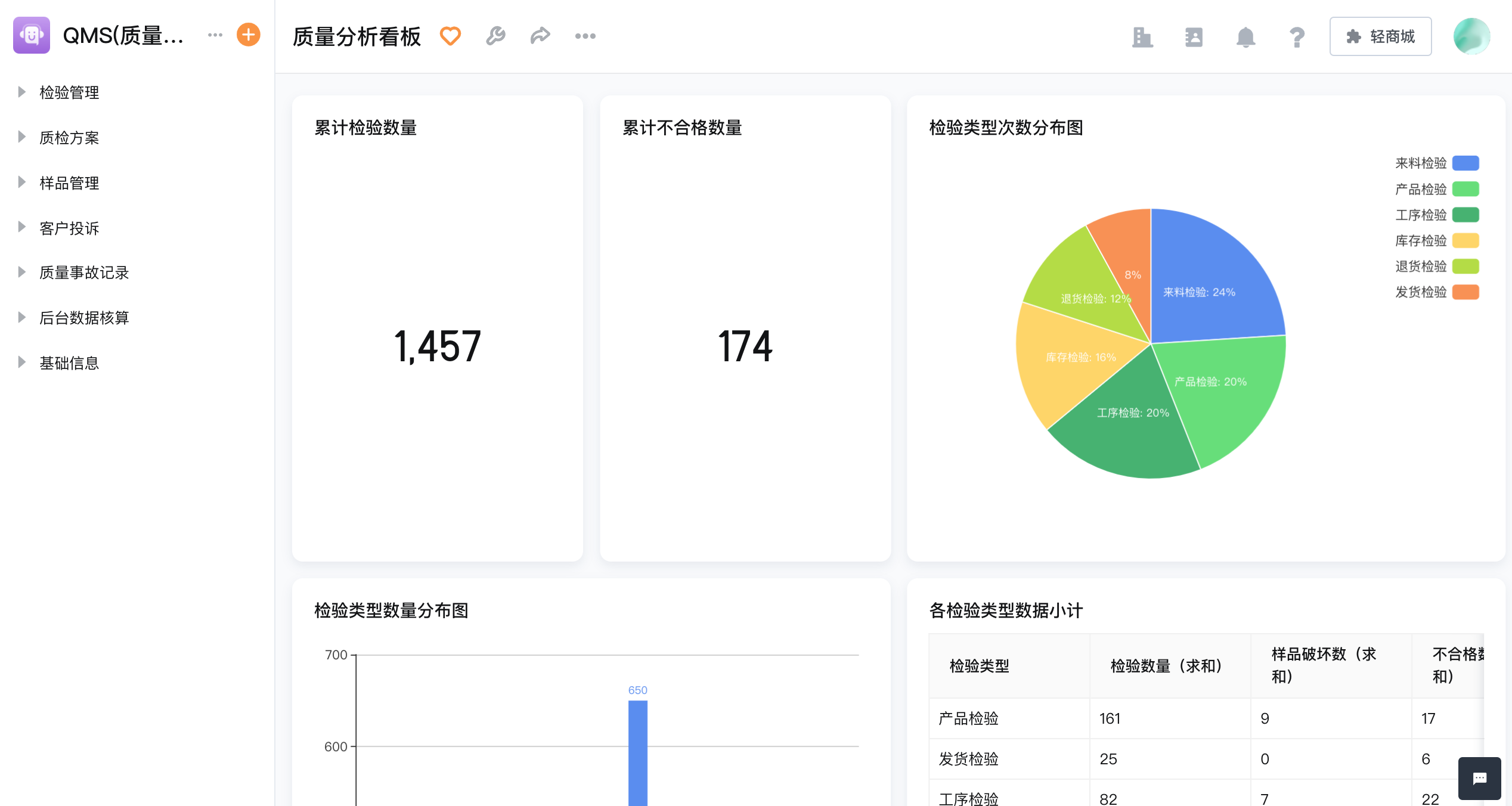
轻流将质量管理划分为四大板块:检验管理(质量管理)、质检方案、样品管理、质量事故记录。
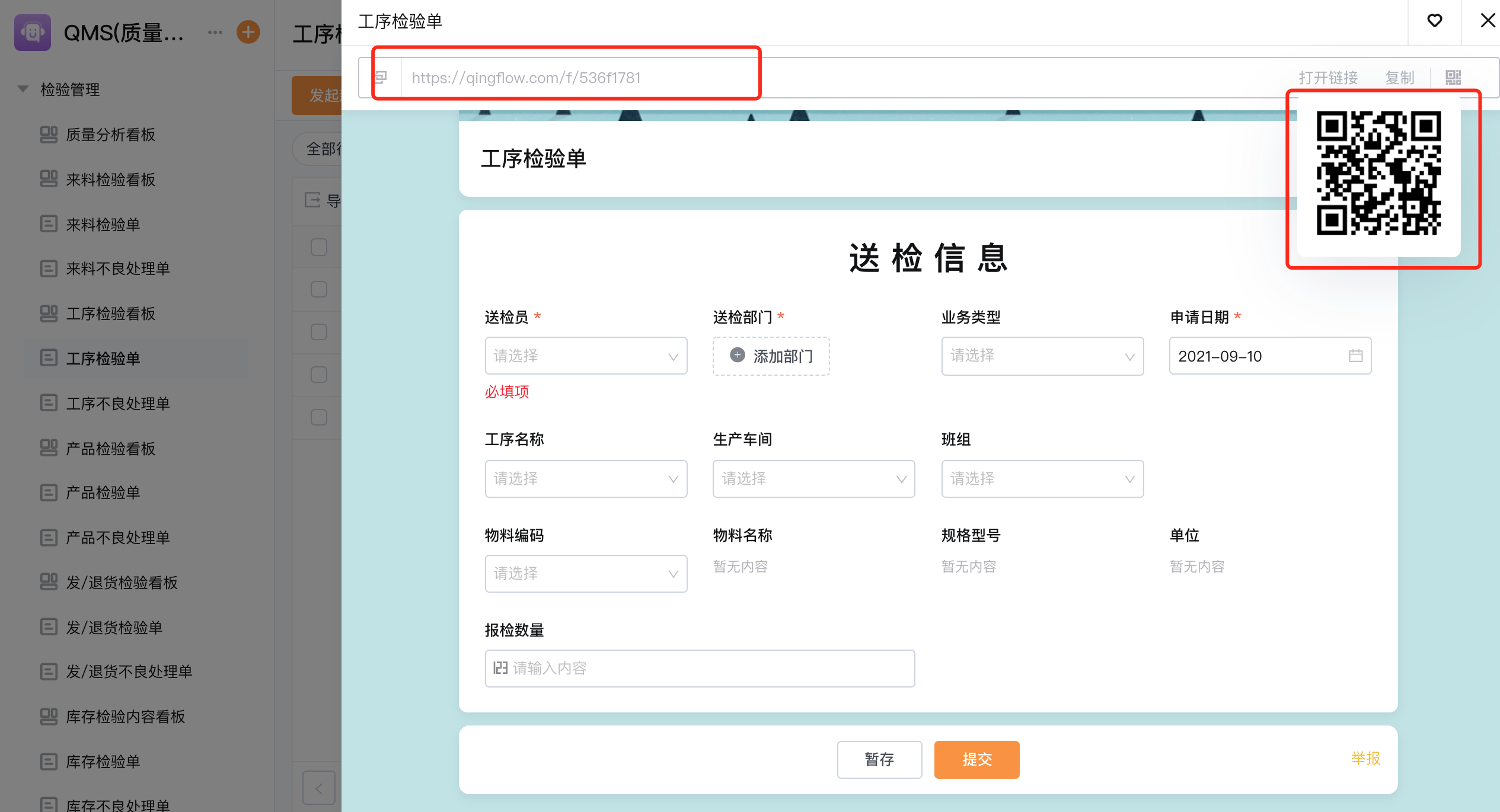
【检验管理】中所有类型的检验单、处理单都可以通过分享链接或扫描二维码的形式直接让员工在手机端、电脑端直接填写,操作方便。
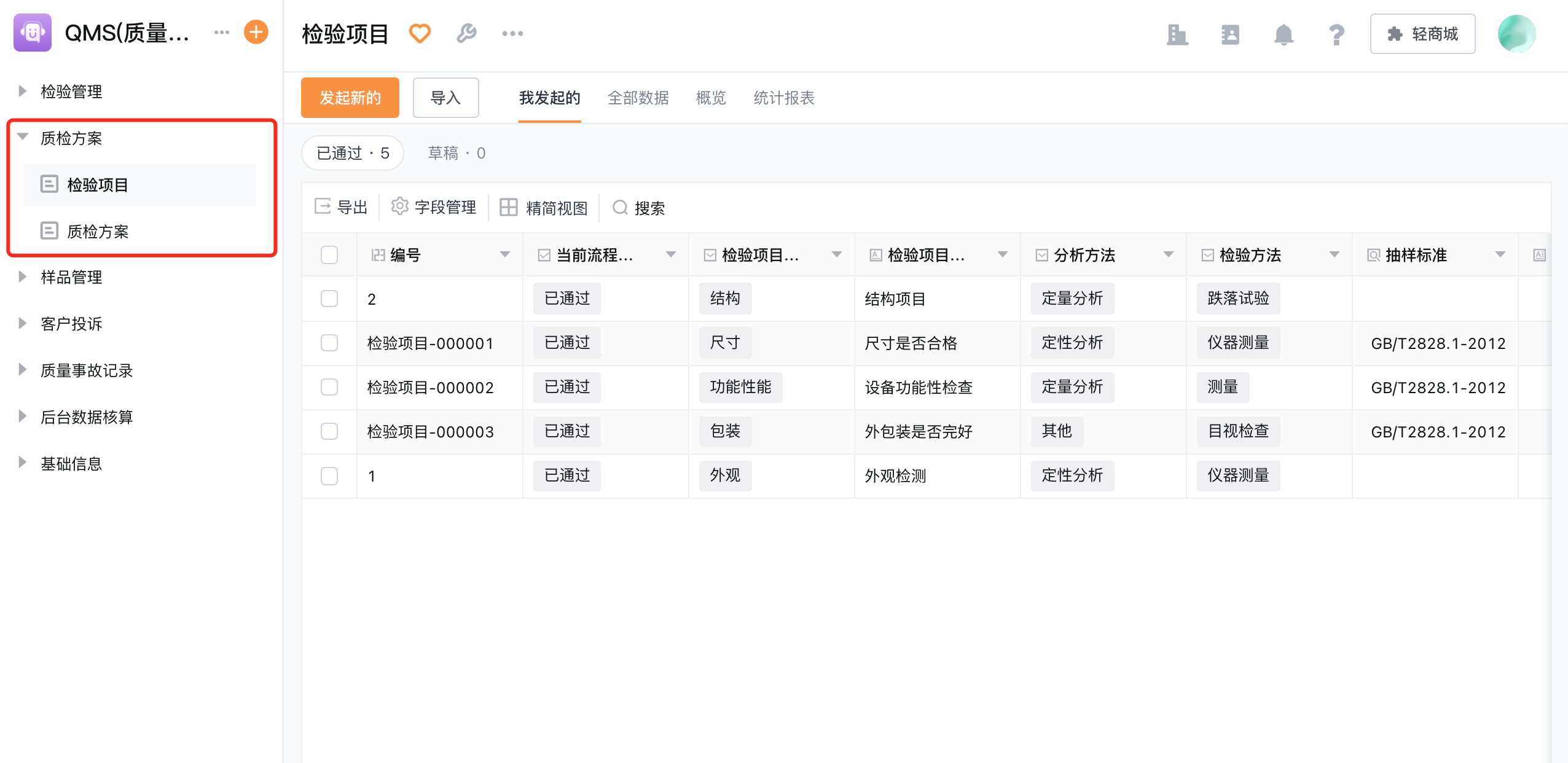
重要的检验项目可以制定【质检方案】,创建完成的检验项目会自动流转至检验员,使用规定的分析方法、检验方法进行检验。
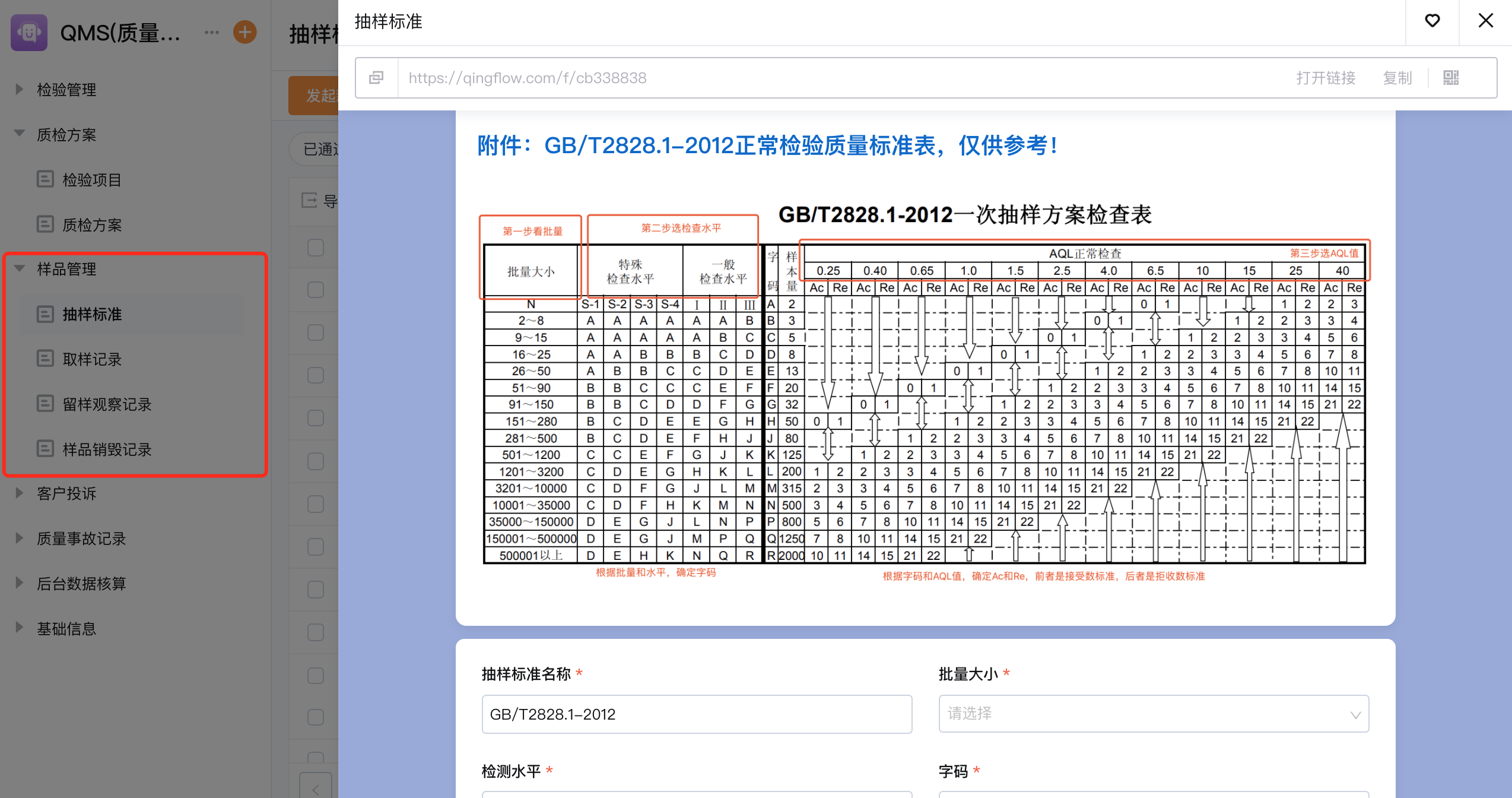
【样品管理】涉及抽样标准、取样记录、留样观察记录、样品销毁记录四个方面,在抽样标准创建表单中提供了GB/T2828.1-2012正常检验质量标准表,以供参考。
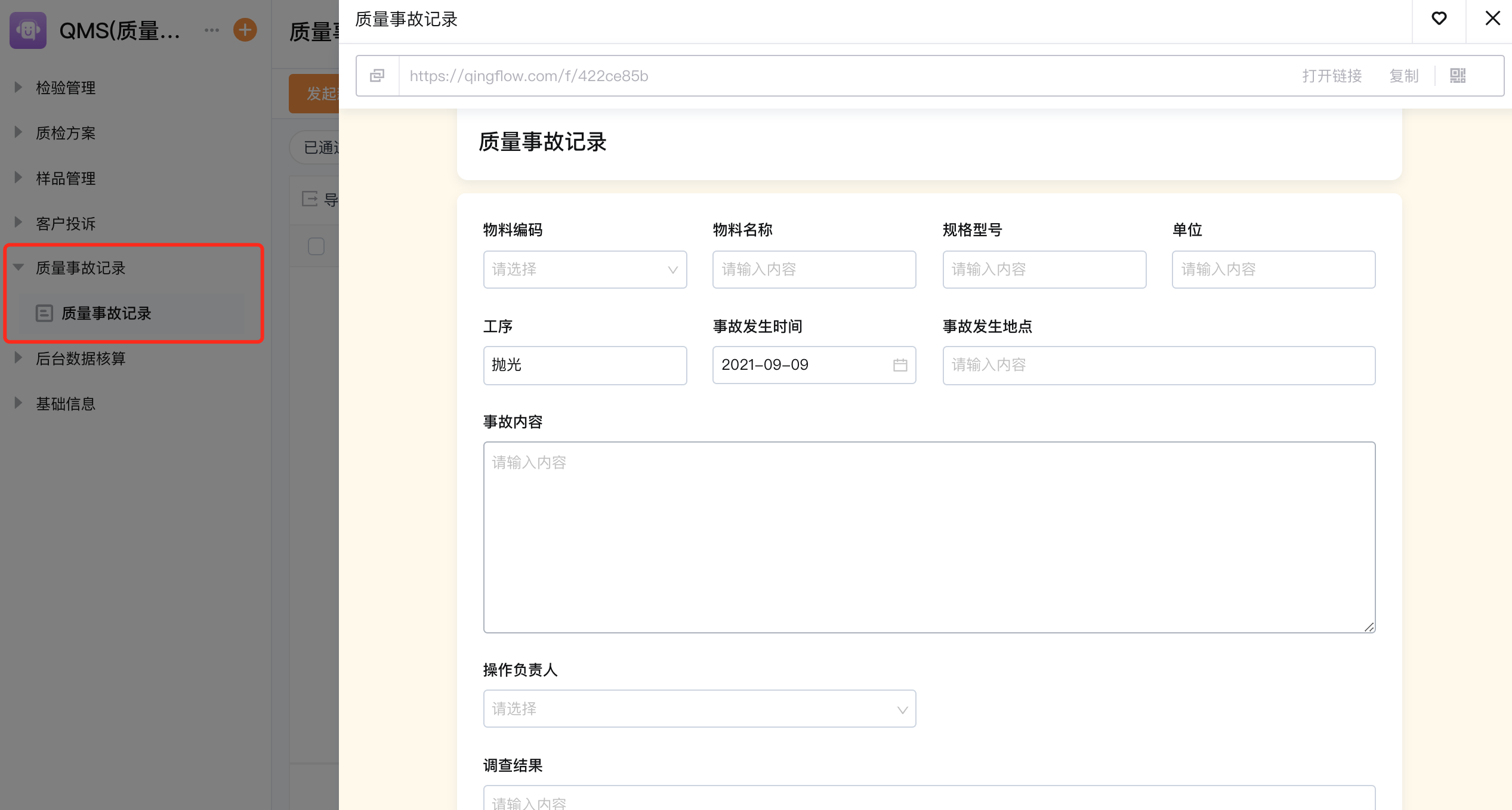
【质量事故记录】可以帮助记录统计质量事故。QMS质量管理系统中检验管理(质量管理)、质检方案、样品管理、质量事故记录模块是精益生产方式中保障质量管理的核心内容,客户投诉、后台数据核算以及基础信息部分可以根据企业实际情况制定自己的质量内容管理板块。

健康安全环境管理系统
安全管理也是精益生产管理不可或缺的一部分,通过隐患排查、安全检查、以及基础信息记录能够及时发现存在的隐患,以免造成损失。
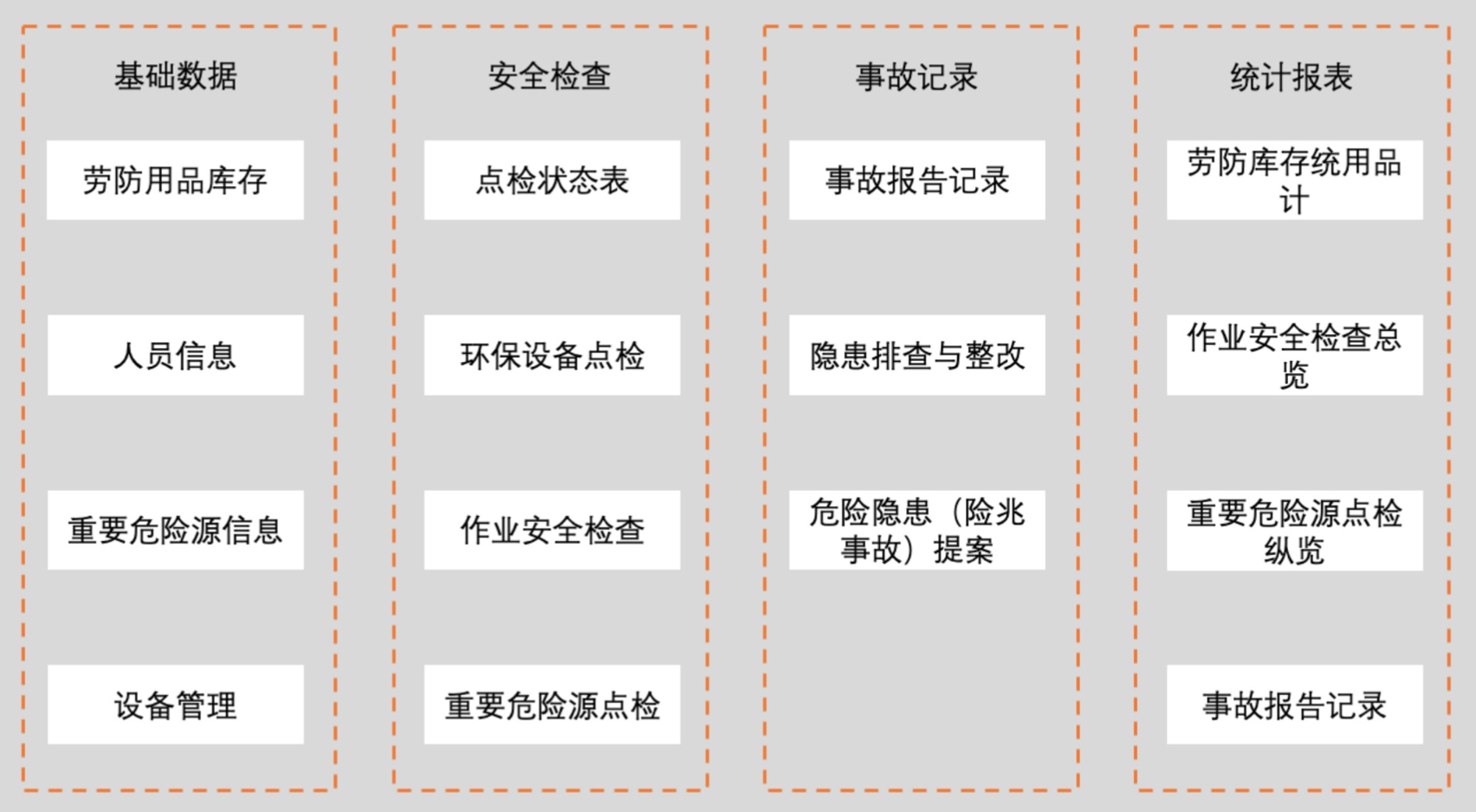
健康安全环境管理系统内覆盖了基础数据、安全检查、事故记录、统计报表四方面内容,将检查和信息相关联,减少重复工作,有效提升效率。
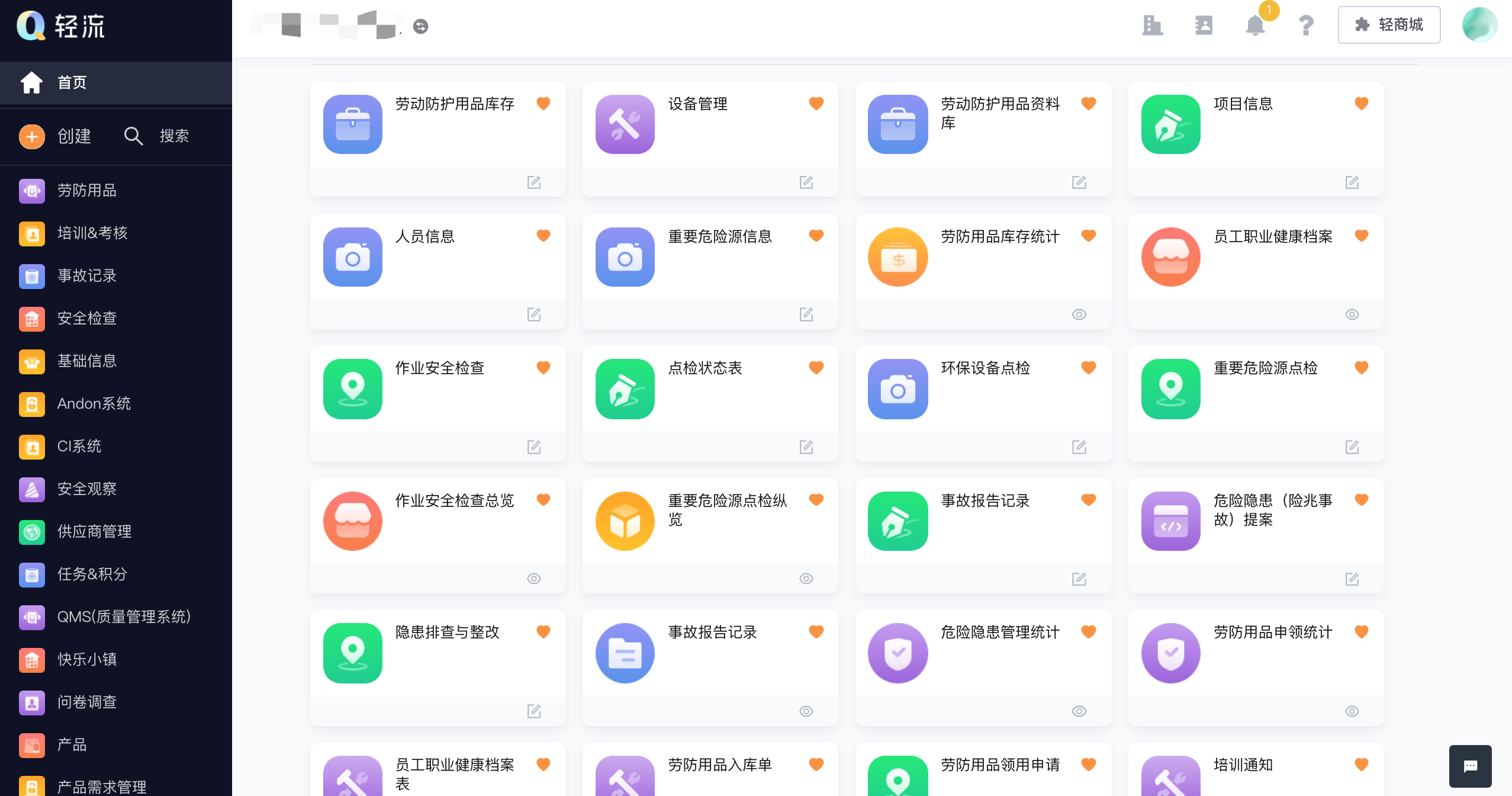
同时,系统内附带了劳保用品的领用和申请,以及相关内容的培训及考试环节,从源头上规范流程,加强员工安全意识,避免事故发生。
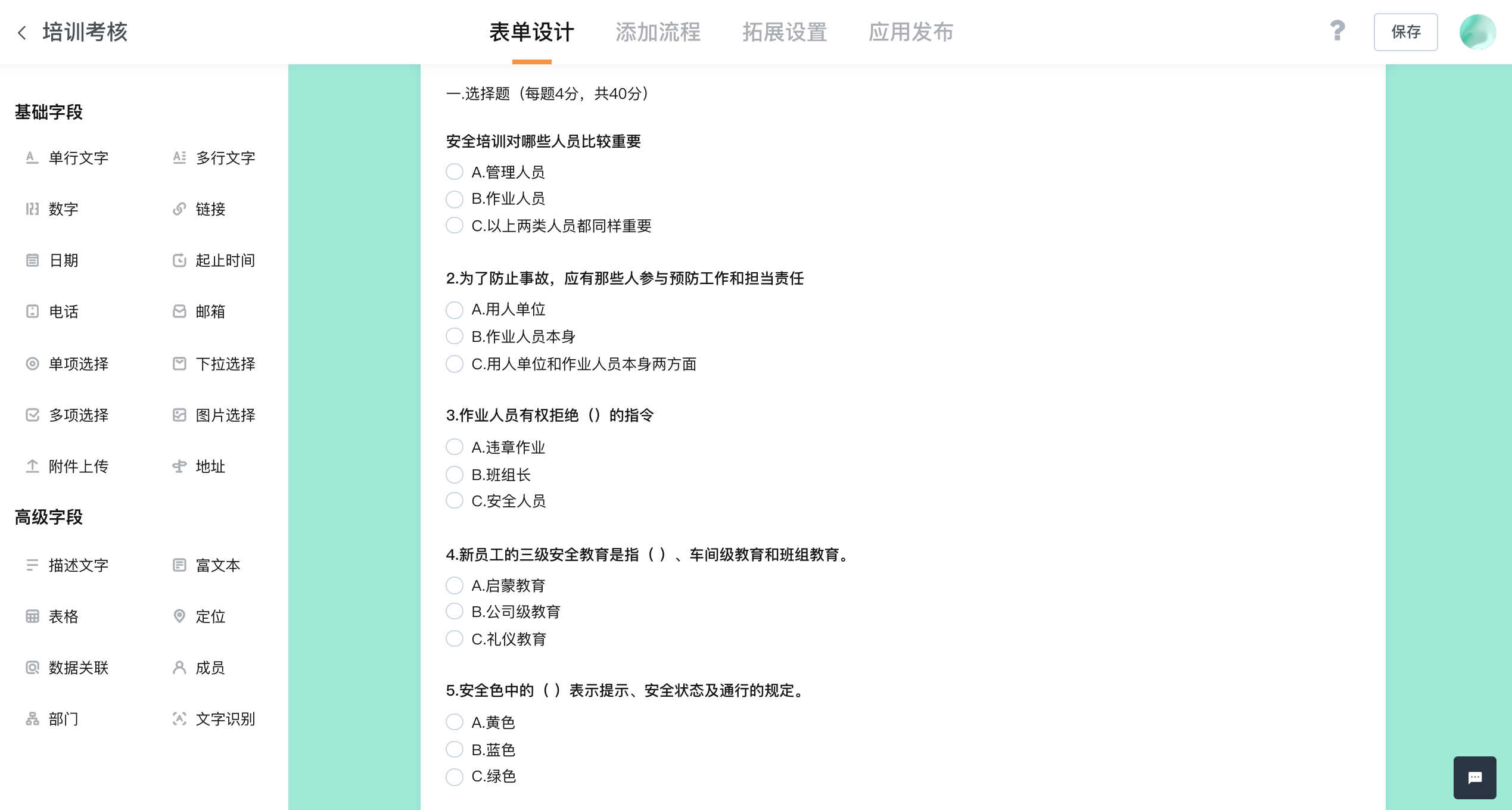
精益生产的数字化实践——案例分享
结合具体的企业案例,进一步感受“数字化”精益生产的便捷与价值。

世界500强企业的精益实践
企业背景:
该家企业在中国有数十家工厂,信息化建设相对完整,且公司领导层十分重视精益生产,全员致力于有效践行精益生产。在多方对比以后,企业选择与轻流合作,推进企业实现数字化精益生产。
落地效果:
最初,先选择有千名员工的a工厂为试点,具体做了CI(合理化建议)、Andon(安灯)、Safety Observation(安全观察)、TPM(全员生产维护)以及销售订单流程管理。
试点成功后进行推广,目前已在十多家工厂落地精益生产管理具体场景,也做了部分系列延伸,比如食堂刷卡、速度门等等。
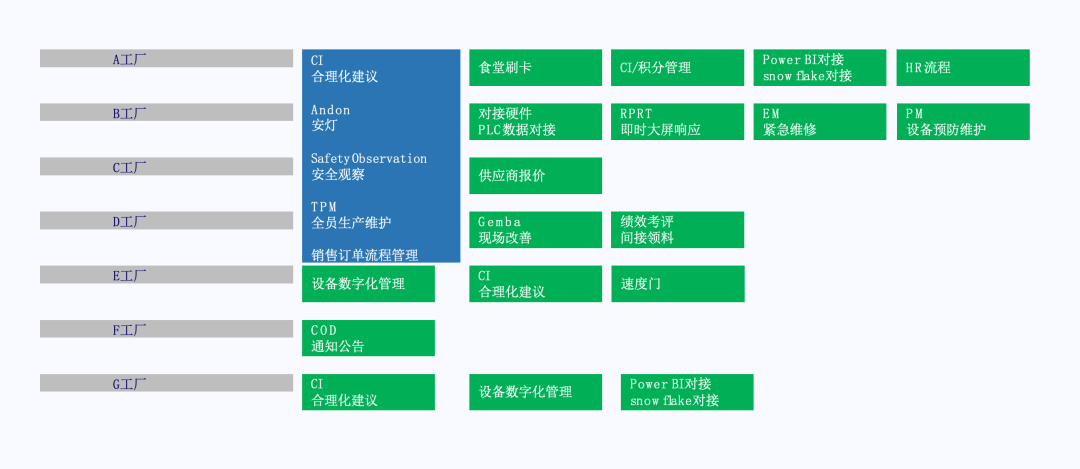
通过轻流打通企业组织架构,实现了全球10万+统一账号打通,顺利对接自己的PowerBI。
基于轻流开发接口,支持前端JSP、SKD布署及开发,通过数据打通,实现SAP、生产、硬件数据联动。
过去,企业的数字化精益生产是通过一面黑板来操作,流程复杂,难以及时跟进;如今,全部迁移至轻流平台进行系统化处理,操作便捷,及时性强。
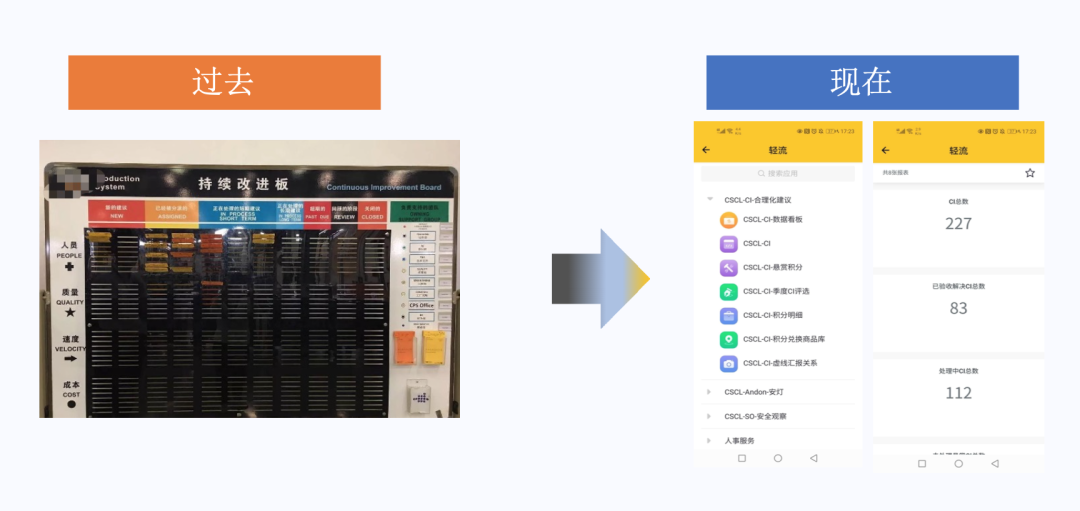
借鉴与思考:
做精益生产的关键性因素就是要取得管理层及一线员工层面的统一认可,这家企业对精益生产的推广方法也具有一定的借鉴意义,比如设置兴趣小组、以奖代罚、重视支持。
轻流平台对客户来说不仅仅是精益生产,也打通了上下游的价值链,包括链接海外集团总部、链接管理层以及一线工人、链接硬件、链接供应商、链接代理商/客户,让未来充满更多想象。
全球领先企业的精益实践
企业背景:
该家企业顺应互联发展浪潮,内部有多套垂直场景SaaS类软件,比如微软全家桶、BPM及低代码平台、SAP、企业微信、OCR系统。但这些系统只能解决某一个场景问题,当企业业务发生变化,就需要进行原系统的二次开发,或者直接采购新的系统去满足。这种业务一发展就要开发系统,购买系统,给企业造成了巨大的IT运维压力。
在这样的情况下,这家企业找到了轻流,决定采用一套面向用户的无代码平台,以此解决信息的流转,打通已有系统,实现数据流闭环,提高IT系统建设效率。
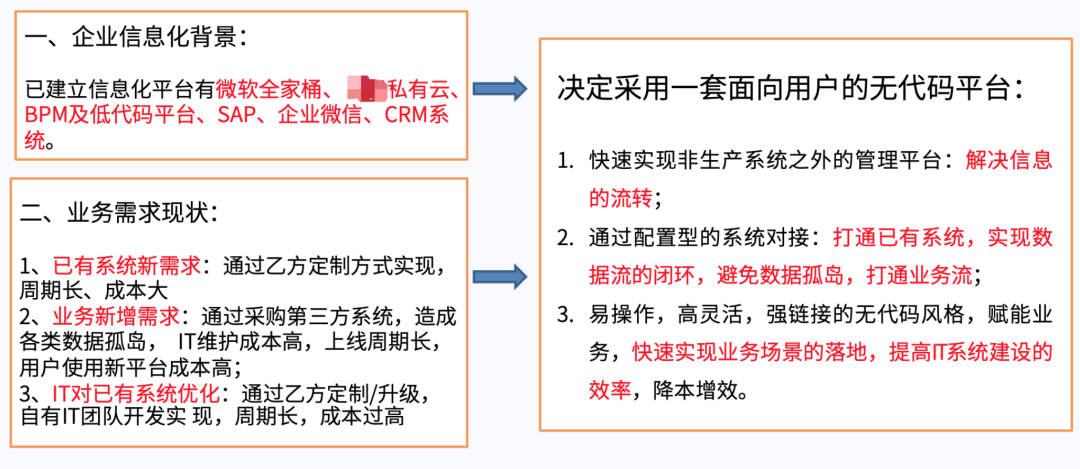
落地效果:轻流借助私有云,打通所有业务系统。既可以把业务系统里的所有数据流转到轻流,也能够通过轻流发起业务数据,反向推送到一系列的业务系统中;下游的精益生产内容赋能给工人,工厂生产数据通过轻流进行分析,直接呈现给管理层。采购方面的成本控制与管理可以链接到下游的供应商,经销商等,与终端的物流用户也可以直接链接。
在2个月周期内,该企业产生892条建议数据, 实现458项优化点,347条待优化中,间接经济价值超过400万。轻流以精益生产的场景落地,与企业实现了更深层次合作,涉及周边所有上下游、终端客户的打通,这是以精益生产为开始,更深层次价值的体现。
国内大部分制造业企业都面临无法快速响应市场需求、任务下发低效出错、采购生产协同效率低、产能利用效率不高、次品率波动大、优化举措缺乏有效追踪等等问题。
精益生产的管理方式能够解决其中大部分问题。轻流精益制造管理数字化解决方案通过无代码系统,使用信息化手段,从接收客户订单起,到进一步的需求分类、库存变量管理、出库质检流程与核验等流程,井井有条地安排整个业务流程。相比传统的ERP,覆盖的业务范围更广,从核心的生产管理到公司的精益管理,都可以通过轻流 · 无代码系统搭建平台解决。
如果这篇文章对你有用的话,欢迎点赞分享评论~
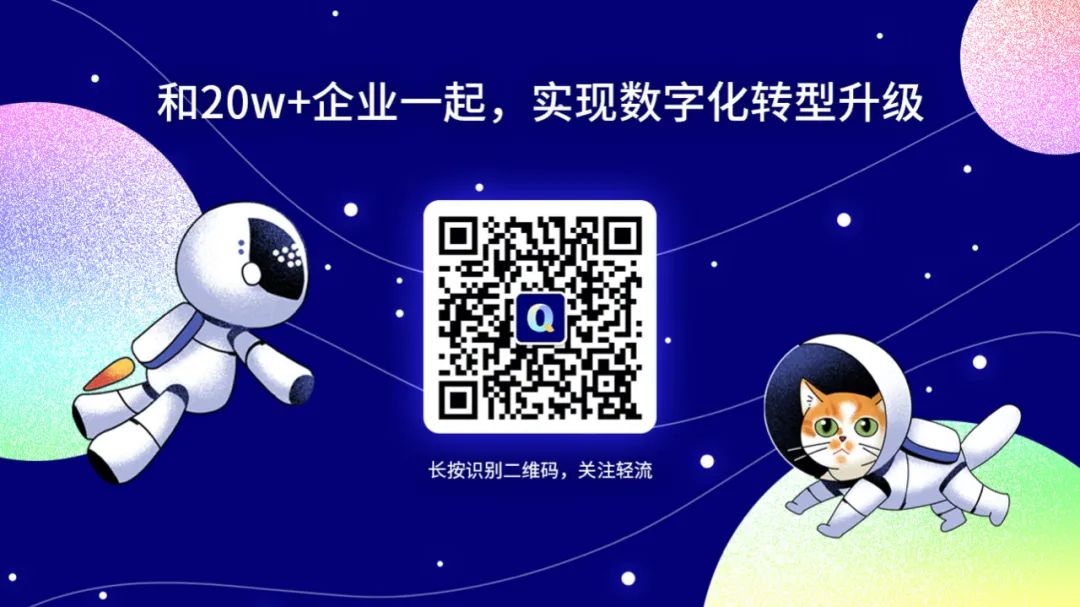